Pharmaceutical Industry
We are a company dedicated to providing comprehensive solutions in the pharmaceutical sector. We have a team of experts in mechanical, electrical, and programming design, providing innovative solutions in sterile processes and equipment sanitization, ensuring quality in the manufacturing and production of high-value pharmaceuticals.
Industrial Process Engineering
Quality and Safety
At Amphora Process Engineering, we adhere to international quality and safety standards, and we have extensive experience in implementing FDA GMP standards, ensuring that our processes comply with all regulations and requirements for pharmaceutical production.
Controlled Environment
Pharmaceutical production processes are carried out in aseptic and controlled environments to prevent contamination and ensure product purity. This includes control of temperature, humidity, and airborne particles.
Specialized and Advanced Equipment
The manufacturing of medications requires specialized machinery and equipment, as well as cutting-edge technologies in automation and process control. These advancements enable greater precision, efficiency, and traceability in production.
Integration of Disciplines
The pharmaceutical industry combines various scientific and technical disciplines such as chemistry, biology, engineering, and information technologies to develop innovative solutions and improve drug production.
Flexibility and Adaptability
Pharmaceutical production must be flexible and adaptable to respond to changing market needs, regulations, and scientific advances. This involves adopting agile and modular production approaches that allow for quick process adjustments.
Cost Reduction and Efficiency
The pressures to reduce costs and improve efficiency in drug production are constant. Companies must optimize their processes, adopt new technologies, and seek ways to increase productivity without compromising quality.
amphora process engineering
Storage
Storage of liquid and solid raw materials in optimal conditions
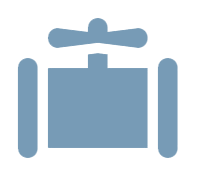
Conduction
Conveyance of liquid and solid raw materials and products according to the required flow rates
Dosing
High-precision dosing of liquid and solid raw materials
Mixing/Agitation
Mixing and agitation of liquid and solid raw materials to achieve a final product
Proyectos “llave en mano” de principio a fin
Purified Water Loops
Purified water, water for injection (WFI), and osmotized water distribution loops in industrial processes require functional solutions and hygienic design to maintain the necessary aseptic conditions.
Firstly, it is important to have adequate filtration and purification systems to remove any contaminants or particles present in the water. This may include activated carbon filters, reverse osmosis systems, and distillation equipment.
Once purified, the water must be stored in suitable tanks or containers that comply with hygiene standards and prevent the proliferation of microorganisms. These containers should be made of stainless steel or similar materials that are easy to clean and disinfect.
For the distribution of purified water, hygienic pipes and distribution systems should be used to prevent water contamination during transport. These pipes should be made of stainless steel or similar materials and should be designed to prevent the accumulation of dirt or microorganisms.
Additionally, it is important to have adequate disinfection systems at the water use points, such as tank or container filling points, to ensure water asepsis at all times. This may include the installation of bactericidal filters or local-level osmosis systems.
In summary, purified water, water for injection (WFI), and osmotized water distribution loops in industrial processes require functional solutions and hygienic design to maintain the required aseptic conditions. This involves the use of adequate filtration and purification systems, hygienic tanks or containers for storage, hygienic pipes and distribution systems, and disinfection systems at water use points.
Guarantee and Reliability in the Design and Construction of all our industrial processes
Certifications (IQ) in Pharmaceutical Industrial Processes
Process certifications, documentation, and design, installation, and operation qualification are standards and procedures used in various sectors to ensure the quality and reliability of products and services.
These certifications and qualifications are important to ensure the quality and reliability of products and services, and to comply with the standards and regulations established in each sector. Additionally, they can
Design Qualification (DQ)
It is carried out during the design stage of a product or process, in order to ensure that all established requirements and specifications are met. This qualification is based on the review of technical documentation and risk analysis.
Installation Qualification (IQ)
It is carried out during the installation stage of equipment, system, or infrastructure, with the aim of verifying that it has been carried out according to established standards and specifications. Installation documentation is reviewed, proper assembly is verified, and tests are performed to ensure proper operation.
Operational Qualification (OQ)
It is carried out during the operation of the system or process, in order to verify that it meets the established requirements and specifications. Tests are conducted and results are analyzed to ensure the proper functioning of the system.
Turnkey Comprehensive Projects
Any product requires the storage of the various ingredients that compose a final product, their dosing, and finally mixing and agitation to achieve the final result.
At Amphora Process, we analyze each component of this formulation to carry out the process with the utmost guarantees in terms of food safety in storage, maximum dosing precision, and perfect mixing to obtain the desired result in the product, always ensuring perfect hygiene at each point.
Request information or a quote from our professionals
Contact Information in Spain
Address
Calle Corretger (pol Industrial Tactica), 17, Paterna, 46980 , Valencia
Phone
+34 960 44 85 50
Contact Information for Mexico, USA, Central America, and the Caribbean
Phone
+52 1 55 9196 8285
javier@amphoraprocess.com
Your data is safe as we comply with the GDPR (General Data Protection Regulation), and here is the information you should know:
Controller: AMPHORA PROCESS ENGINEERING, S.L.
Controller’s Address: CORRETGER, 17 POL. IND. TACTICA 46988 PATERNA
Purpose: To address your requests and provide our services.
Legitimation: We will only process your data with your prior consent, which you can provide by checking the corresponding box established for this purpose.
Recipients: In general, only the staff of our organization who are duly authorized may have knowledge of the information we request from you.
Rights: To know what information we have about you, correct it, and delete it, as explained in the additional information available on our website.